Wskazane jest ciągłe monitorowanie lub przynajmniej okresowe sprawdzanie parametrów energetycznych pomp. W praktyce, na stanowisku pracy, pomiar wysokości podnoszenia, mocy i ciężaru właściwego jest stosunkowo prosty i możliwy do przeprowadzenia z wysoką dokładnością. Natomiast precyzyjny pomiar wydajności jest już problematyczny. Bez niego nie da się jednak precyzyjnie oszacować aktualnej sprawności pompy uwzględniającej pogorszenie stanu technicznego na skutek zużycia.
W trakcie eksploatacji pompy wskazane jest ciągłe monitorowanie lub okresowe sprawdzanie jej parametrów energetycznych w celu upewnienia się, czy pracuje ona z optymalną sprawnością. Jest to istotne nie tylko ze względów technicznych, lecz również ekonomicznych, gdyż koszty energii do napędu pompy są znaczące w całkowitym koszcie pompowania.
Koszty energii i sprawność w rzeczywistym punkcie pracy.
Z punktu widzenia kosztu energii ważna jest nie tyle maksymalna sprawność, jaką pompa może osiągnąć w optymalnym punkcie charakterystyki, lecz sprawność w rzeczywistym punkcie pracy. Zagadnienie staje się bardziej złożone gdy punkt pracy jest zmienny, gdyż wtedy o efektywności energetycznej układu decyduje zastosowana metoda regulacji. W prostszym przypadku, gdy punkt pracy jest w przybliżeniu stały, straty energii wynikają głównie z dwóch przyczyn:
-
Niewłaściwy dobór pompy do układu w wyniku czego pracuje ona ze sprawnością niższą od maksymalnej. Wynika to albo z błędu w doborze (np. niewłaściwe oszacowanie strat przepływu lub przyjęcie zbyt wysokiej nadwyżki parametrów) albo ze zmiany parametrów, jaka nastąpiła od czasu zaprojektowania układu. Ta druga sytuacja jest często spotykana w praktyce.
-
Obniżona sprawność prawidłowo dobranej pompy. Obniżenie może wynikać z dostarczenia pompy niewłaściwie wykonanej, o sprawności niższej niż oferowana lub z pogorszania stanu technicznego pompy na skutek zużycia. Tempo zużycia zależy od wielu czynników, jak przede wszystkim rodzaj pompowanego medium, prędkość obrotowa i dobór wykonania materiałowego. Niezależnie od warunków pracy, po kilku latach eksploatacji należy się spodziewać dostrzegalnego pogorszenia sprawności. Efekt ten często pozostaje niezauważony w przypadku automatycznej regulacji prędkości obrotowej. Jeśli pompa pracuje ze stałą prędkością obrotową, to na skutek zużycia jej wydajność z czasem maleje i użytkownik podejmuje decyzje o remoncie, gdyż pompa nie spełnia już swojej funkcji. Natomiast w przypadku automatycznej regulacji, efekt zużycia jest kompensowany przez zwiększanie prędkości obrotowej, w wyniku czego pompa utrzymuje wymagane ciśnienie lub wydajność, co jednak odbywa się kosztem zwiększonego zużycia energii.
Oczywiście, w praktyce często zachodzi kombinacja obu wymienionych wyżej czynników.
W każdym przypadku zalecana jest okresowa weryfikacja energochłonności pompy pracującej w danym układzie, co można przeprowadzić, dokonując pomiarów jej parametrów energetycznych. W rezultacie, na podstawie wyników, można ocenić poziom energochłonności zespołu pompowego, możliwe do uzyskania oszczędności energetyczne oraz oszacować efekty ekonomiczne ewentualnej modernizacji. Na tej podstawie można podejmować decyzje dotyczące inwestycji w poprawę efektywności układów pompowych (np. poprzez ich modernizacje lub remonty) na podstawie rzetelnej analizy techniczno-ekonomicznej. Bez danych pomiarowych decyzje takie muszą być podejmowane do pewnego stopnia intuicyjnie, co stwarza ryzyko przeznaczenia nakładów inwestycyjnych na przedsięwzięcia nie gwarantujące uzyskania oczekiwanych efektów.
Możliwość przeprowadzenia pomiarów parametrów energetycznych pomp na stanowisku pracy.
Dla oceny sprawności zespołu pompowego należy zmierzyć:
a) wydajność,
b) wysokość podnoszenia,
c) pobór mocy,
d) ciężar właściwy pompowanego medium.
W praktyce, na stanowisku pracy, pomiar wysokości podnoszenia, mocy i ciężaru właściwego jest stosunkowo prosty i możliwy do przeprowadzenia z wysoką dokładnością. Natomiast precyzyjny pomiar wydajności jest problematyczny. Metody pomiaru wydajności oraz towarzyszące temu problemy opisane są m.in. w [1, 2]. Niezależnie od rodzaju użytego przepływomierza uzyskanie dokładnych wyników wymaga przeprowadzenia pomiarów na prostym odcinku rurociągu. Zazwyczaj wymaga się odcinka prostego o długości 15 średnic, aczkolwiek producenci niektórych typów przepływomierzy dopuszczają odcinki krótsze. Wynika to z tego, że algorytmy stosowane do przeliczania zmierzonej wielkości fizycznej na wynik w postaci natężenia przepływu oparte są o założenie, że w rurociągu występuje ustabilizowany profil prędkości, zbliżony do prostokątnego. Jeśli przed przepływomierzem znajdują się elementy zakłócające przepływ (kolana, armatura, zmiany przekroju, itp.) bądź generujące zawirowania, to rozkład prędkości w miejscu pomiaru różni się od zakładanego i pomiar obarczony jest błędem. Dodatkowo, jeśli w układzie pompowym nie jest na stałe zabudowany przepływomierz, to do pomiarów wydajności używa się tzw. przepływomierzy bezinwazyjnych, najczęściej ultradźwiękowych. Pomiaru dokonuje się przy zastosowaniu głowic pomiarowych przykładanych do zewnętrznych ścianek rurociągu. W takim przypadku wprowadzana jest dodatkowa niepewność pomiarowa wynikająca ze stanu ścianek rurociągu. Ewentualne osady zakłócają sygnał ultradźwiękowy i powodują zwiększenie błędów pomiarowych. Jeśli pomiar wydajności w bardziej złożonym układzie pompowym nie jest dokonywany bezpośrednio na rurociągu tłocznym mierzonej pompy, lecz np. na kolektorze zbiorczym zasilanym przez kilka pomp, to powstaje wątpliwość co do tego, czy zmierzona wydajność odpowiada ściśle wydajności pompy. Na skutek braku pełnej szczelności armatury odcinającej mogą bowiem występować przecieki, np. przepływy powrotne przez pompy połączone równolegle z badaną, co skutkuje obniżeniem wyniku pomiaru.
Niepewności pomiarowe i sposoby ich ograniczania.
Dokładność pomiarów przeprowadzanych na stanowisku pracy zależy od konfiguracji układu (występowanie odcinków prostych rurociągów, stan ścianek), klasy stosowanych przyrządów pomiarowych oraz doświadczenia osób prowadzących pomiary. Nawet w sprzyjających warunkach należy się liczyć z błędami rzędu kilku procent wynikającymi głównie z niedokładnego pomiaru wydajności. Z tego względu norma [3] zaleca, aby pomiary odbiorcze nowych pomp lub pomp po kapitalnym remoncie odbywały się nie na stanowisku pracy lecz na specjalnym stanowisku pomiarowym, którym powinien dysponować producent lub wykonawca remontu. Aby wykluczyć ewentualne wątpliwości co do rzetelności pomiarów prowadzonych przez producenta lub wykonawcę remontu, można je przeprowadzić pod nadzorem wyspecjalizowanej firmy trzeciej.
Dla porządku należy dodać, że istnieją metody pomiaru wydajności, jak np. metoda izotopowa, pozwalające ograniczyć niepewność pomiarową również w przypadku braku odcinków prostych rurociągów oraz wobec nieznanego stanu ich ścianek. Metody takie, ze względu na stopień skomplikowania oraz koszt znajdują jednak zastosowanie głównie dla układów pompowych o najwyższych parametrach (wysokie wydajności i moce) i nie są stosowane na szeroką skalę.
Z faktu, że obowiązujący standard techniczny [3] nie zaleca przeprowadzania pomiarów odbiorczych na stanowisku pracy, nie należy wyciągać wniosku, że pomiarów takich nie należy prowadzić w ogóle. Przeciwnie, ze względów omówionych wyżej okresowa ocena efektywności energetycznej danego układu pompowego jest wskazana. Jak stwierdzono, należy liczyć się z co najmniej kilkuprocentową niepewnością pomiarową, lecz nawet taka dokładność pozwala na uzyskanie przydatnych wniosków co do celowości modernizacji lub remontu.
Niepewność pomiarową można w znacznej mierze ograniczyć, jeśli na etapie projektowania układu pompowego możliwość prowadzenia pomiarów zostanie wzięta pod uwagę. W idealnym przypadku należy przewidzieć zabudowę na stałe przepływomierzy dla poszczególnych pomp z uwzględnieniem wymaganych odcinków prostych rurociągów, co pozwala na ciągłe monitorowanie sprawności. Jeśli ze względów ekonomicznych takie rozwiązanie nie jest możliwe to jako minimum należy zaprojektować co najmniej odcinek prosty rurociągu o wymaganej długości dla pomiarów wydajności. Na odcinku takim można zainstalować demontowalny odcinek pomiędzy kołnierzami, który na okres pomiarów można zastąpić przepływomierzem. Jeśli planuje się korzystanie z przepływomierzy bezinwazyjnych, to wskazana jest możliwość wymiany całego prostego odcinka pomiarowego celem wyeliminowania wątpliwości co do stanu ścianek.
W przypadku gdy projektant instalacji weźmie pod uwagę wszystkie zalecenia normy [3] oraz gdy na realizację projektu przeznaczone zostaną odpowiednie nakłady możliwe jest prowadzenie pomiarów na stanowisku pracy z dokładnością odpowiadającą wymaganiom [3]. W chwili obecnej zaprojektowane w taki sposób układy pompowe należą jednak do rzadkości.
Ocena parametrów pomp bez możliwości przeprowadzenia precyzyjnych pomiarów.
Jeżeli dokładne pomiary na stanowisku pracy nie są możliwe (co, jak stwierdzono wyżej, spowodowane jest najczęściej trudnościami przy pomiarze wydajności) do oceny punktu pracy pompy można wykorzystać charakterystykę pompy sporządzoną podczas prób odbiorczych. Jeśli chcemy wyciągać na takiej podstawie dokładne wnioski, to nie powinna to być charakterystyka typu pompy ani uśredniona charakterystyka ofertowa, lecz charakterystyka konkretnego egzemplarza, która od charakterystyki typu może się różnić o dopuszczalne tolerancje. Należy pamiętać, że charakterystyka H(Q) wyliczana jest na podstawie wyników pomiarów ze wzoru:
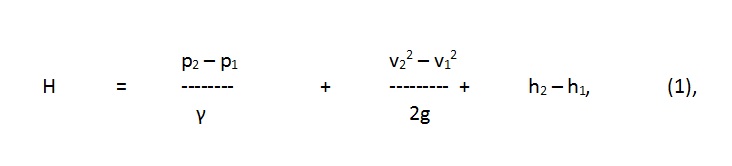
gdzie indeksem 2 oznaczone są parametry na wylocie, a indeksem 1 parametry na wlocie do pompy. (p oznacza ciśnienie, v prędkość, a h wysokość punktu pomiaru ciśnienia ponad przyjęty poziom odniesienia).
W praktyce dominujące znaczenie ma pierwszy człon (różnica ciśnień pomiędzy wylotem a wlotem podzielona przez ciężar właściwy). Jeśli znamy różnicę wysokości pomiędzy punktami pomiaru ciśnienia oraz średnice rurociągów na ssaniu i tłoczeniu, to charakterystykę H(Q) wyliczoną na podstawie wzoru (1) możemy skorygować tak, aby uzyskać zależność Δp (Q), gdzie Δp = p2 – p1.
Następnie, mierząc Δp = p2 – p1, możemy wyciągać wnioski co do położenia punktu pracy, czyli aktualnej wydajności.

Rys. 1. Ocena położenia punktu pracy pompy na podstawie pomiaru H.
Dla przykładu weźmy pod uwagę współpracę pompy o charakterystyce H(Q) pokazanej na rys. 1 linią ciągłą z układem, którego charakterystyka Hukł (Q) pokazana jest linią przerywaną. Pompę dobrano tak, aby jej punkt pracy wypadł w punkcie przecięcia jej charakterystyki z charakterystyką układu, tzn. przy parametrach Hn, Qn. Załóżmy, że po zainstalowaniu pompy na stanowisku pracy podczas pomiarów kontrolnych zmierzono Δp = p2 – p1 , która to wartość po skorygowaniu o dwa ostatnie człony we wzorze (1) okazała się równa H1, a zatem niższa od Hn. Jeśli możemy mieć pewność co do przebiegu charakterystyki pompy, to wyciągamy stąd wniosek, że pracuje ona z wydajnością Q1 wyższą od Qn. W przypadku pompy o rosnącym z wydajnością poborem mocy dobranej na sprawność maksymalną przy wydajności Qn, jak na rys. 1, praca przy wydajności zwiększonej do Q1 odbywać się będzie z obniżoną sprawnością i zwiększonym poborem mocy, a zatem z obniżoną efektywnością energetyczną. Jako prawdopodobną przyczynę tego zjawiska można wskazać to, że rzeczywiste opory przepływu w układzie pompowym okazały się niższe od zakładanych na etapie projektu (linia kreskowo-kropkowa przebiegająca poniżej linii przerywanej oznaczającej Hukł), na skutek czego pompa o określonej charakterystyce „przesunęła się” na wyższą wydajność. Aby zmniejszyć wydajność do zakładanej wartości Qn i poprawić efektywność, należałoby dokonać korekty średnicy wirnika.
W taki sposób można wyciągnąć istotne z punktu praktycznego wnioski bez pomiaru wydajności, wyłącznie na podstawie pomiaru ciśnienia. Będą one słuszne, o ile charakterystyka pompy jest dokładna. Można tak założyć w przypadku pompy nowej lub będącej w eksploatacji od stosunkowo niedługiego czasu. Natomiast po pewnym okresie eksploatacji na skutek zużycia charakterystyka pompy ulega obniżeniu (parametry pompy spadają). Wtedy, jeśli stwierdzimy na podstawie pomiarów spadek Δp nie jesteśmy już w stanie wyciągnąć jednoznacznych wniosków. Obniżenie Δp może bowiem wynikać nie tylko, jak dla nowej pompy, ze zmniejszonych oporów w układzie, lecz może także być skutkiem obniżenia charakterystyki pompy. Jeśli na skutek pogorszenia stanu technicznego charakterystyka pompy obniżyła się tak, jak pokazuje linia poniżej fabrycznej charakterystyki H(Q), a charakterystyka układu jest taka jak zakładano, to punkt pracy w wyniku przecięcia charakterystyk ustali się przy mniejszej wydajności Q2, a ustalona na podstawie pomiaru Δp wysokość podnoszenia nadal będzie wynosić H1. Spadek zmierzonej wysokości podnoszenia może zatem wynikać zarówno z obniżenia oporów układu, jak i z obniżenia parametrów pompy, jak również z łącznego wpływu obu czynników, przy czym ich rozdzielenie jest trudne. Da się w tym zakresie uzyskać pewne wnioski o charakterze jakościowym. Jeśli bowiem obniżenie wysokości podnoszenia wynika z obniżenia oporów układu, to pompa o charakterystyce P(Q), jak na rys. 1, wykaże wzrost poboru mocy. Natomiast jeśli pompa na skutek zużycia wykazuje spadek wysokości podnoszenia, to najczęściej towarzyszy temu również spadek poboru mocy. Zatem mierząc oprócz przyrostu ciśnienia wytwarzanego przez pompę również jej pobór mocy możemy wyciągnąć wnioski co do jej stanu technicznego. Należy jednak podkreślić, że bez pomiaru wydajności nie da się precyzyjnie określić aktualnej sprawności pompy na stanowisku pracy. Analizując zgodność lub ewentualne rozbieżności pomiarów wysokości podnoszenia i mocy w stosunku do charakterystyki fabrycznej, da się jedynie jakościowo ocenić, czy pompa odbiega od początkowego stanu, natomiast bez pomiaru wydajności nie da się precyzyjnie ocenić aktualnego poziomu sprawności.
Można przyjąć założenie, że charakterystyka układu zmienia się o wiele wolniej niż charakterystyka pompy, co znajduje uzasadnienie w fakcie, że elementy pompy zużywają się szybciej niż elementy rurociągu, gdyż w pompie występują o wiele wyższe prędkości przepływu cieczy. Przy takim założeniu dałoby się pewien odcinek rurociągu wycechować jako orientacyjny przepływomierz. Po zainstalowaniu pompy, mierząc wytwarzany przez nią przyrost ciśnienia dałoby się z jej charakterystyki fabrycznej ustalić wydajność. Jednocześnie mierząc spadek ciśnienia na określonym odcinku rurociągu przy tej znanej wydajności, dałoby się oszacować współczynnik oporu, zakładając, że strata ciśnienia jest proporcjonalna do kwadratu wydajności Δp = a Q2. Mając w taki sposób oszacowany współczynnik oporu a, dałoby się następnie na podstawie pomiaru spadku ciśnienia oceniać wydajność przepływającą przez ten odcinek rurociągu, co by w dalszej kolejności służyło ocenie stanu pompy. Metoda taka będzie jednak nieprzydatna w sytuacji gdy na ściankach rurociągu w miarę upływu czasu powstają osady, co wyklucza założenie o niezmienności oporów przepływu.
Należy podkreślić, że szacunkowe metody oceny stanu pompy, podobne jak opisana wyżej, mogą dostarczyć wniosków o charakterze jakościowym, o ile analizy takie prowadzone są przez osoby dysponujące odpowiednią wiedzą i doświadczeniem. Mogą się one okazać przydatne do wstępnej oceny sytuacji, lecz zawsze będą obarczone błędami i nie będą w stanie dostarczyć precyzyjnych informacji na temat stanu zużycia pompy i jej aktualnej sprawności. Zatem, jeśli w instalacji nie ma możliwości pomiaru wydajności, dokładne informacje o stanie technicznym pompy można uzyskać jedynie kierując ją na badania na odpowiednie stanowisko badawcze, np. u producenta.
Podsumowanie.
Ze względu na efektywność energetyczną wskazane jest ciągłe monitorowanie lub przynajmniej okresowe pomiary parametrów energetycznych pomp. Możliwość takich ciągłych lub okresowych pomiarów powinna być przewidziana na etapie projektowania układu pompowego. W szczególności wskazane jest zabudowanie przepływomierza lub, przynajmniej, zapewnienie warunków do jego czasowej zabudowy na okres pomiarów.
Jeśli w układzie pompowym nie ma warunków do prowadzenie dokładnych pomiarów wydajności, to ocenę dopasowania pompy do układu można przeprowadzić po jej zainstalowaniu na podstawie dokładnej charakterystyki fabrycznej.
Bez pomiaru wydajności nie da się precyzyjnie ocenić aktualnej sprawności pompy uwzględniającej pogorszenie stanu technicznego na skutek zużycia. Doświadczone osoby mogą dokonywać przybliżonych oszacowań w tym zakresie kierując się dostępnymi, częściowymi wynikami pomiarów. Oszacowania takie będą jednak w każdym przypadku obarczone niepewnością. Zalecaną praktyka byłoby kierowanie pompy na badania na specjalistycznym stanowisku jeśli orientacyjne oceny sugerują pogorszenie stanu technicznego pompy. Dokładne pomiary w takim przypadku dostarczyłyby precyzyjnych argumentów za skierowaniem pompy do remontu lub modernizacji.
dr inż. Grzegorz Pakuła
1. M. Cichoń, Bezinwazyjne pomiary przepływu, czyli rozprawa z mitami – cz. 1, Pod Kontrolą, 04/2014 (30).
2. M. Cichoń, Bezinwazyjne pomiary przepływu, czyli rozprawa z mitami – cz. 2, Pod Kontrolą, 01/2015 (31).
3. Norma PN-EN ISO 9906, Pompy wirowe – badania odbiorcze parametrów hydraulicznych – Klasy dokładności 1,2 i 3, czerwiec 2012.