1. WPROWADZENIE.
Zużycie energii do napędu pomp stanowi poważną pozycję w sumie zużycia energii na potrzeby własne bloku energetycznego. Dla przykładu, w przypadku bloków energetycznych o mocy 200 MW suma poboru mocy pracujących w nim pomp sięga 10 MW czyli 5% mocy bloku.
Największy pobór mocy wykazują pompy zasilające kocioł. W typowym rozwiązaniu bloku 200 MW stosowanym w polskiej energetyce pompy zainstalowane są w układzie 3 x 50%, to znaczy dwie pracujące równolegle pompy dają wymaganą wydajność, a trzecia pompa stanowi rezerwę. Pobór mocy każdej z dwu pracujących pomp zasilających jest rzędu 3 MW. Tak znaczny pobór mocy jest w pewnym stopniu nieunikniony gdyż wynika z konieczności podniesienia ciśnienia na określonym etapie obiegu termodynamicznego stanowiącego podstawę generacji energii w elektrowni cieplnej. Rzeczywisty pobór mocy przewyższa jednak niezbędne z punktu widzenia fizyczne minimum z powodu tego, że sprawność zespołu pompowego jest niższa od stu procent. Utrzymywanie tej sprawności na możliwie wysokim poziomie stwarza możliwość redukcji zużycia energii na potrzeby własne bloku energetycznego.
2. SPRAWNOŚĆ ZESPOŁÓW POMPOWYCH.
Pompy zasilające pracujące w elektrowniach są na ogół wyposażone w przyrządy pozwalające na pomiar podstawowych parametrów (wydajność, ciśnienie, pobór prądu silnika), na podstawie wskazań których można oszacować sprawność zespołu pompowego. Są to pomiary o dokładności przemysłowej, nie dające w pełni wymaganej dokładności lecz pozwalające na ocenę rzędu wielkości. Na rys. 1 pokazany jest uzyskana na podstawie pomiarów przykładowa zależność sprawności od wydajności zespołu pompowego, która powiązana jest bezpośrednio z obciążeniem bloku. Wyniki pokazane na rysunku można uznać za nieco lepsze od przeciętnych gdyż spotyka się dane z innych elektrowni wykazujące niższy poziom sprawności.
W celu oceny takiego stanu można przyjąć, że nowa pompa zasilająca tego typu powinna posiada sprawność rzędu 81%, natomiast silnik z okresu gdy zespół pompowy był instalowany powinien posiadać sprawność rzędu 94%. Jak z tego wynika oczekiwana sprawność zespołu pompowego powinna wynosić 0.81 x 0.94 = 76.1 %. Jak widać na rys.1 rzeczywista sprawność zespołu jest o ok. 10% niższa. Różnica ta powoduje nadmierne straty, eliminacja których umożliwia redukcję zużycia energii na potrzeby własne bloku. Poniżej omówione zostaną źródła strat oraz wskazane zostaną możliwości ich ograniczenia.

Rys. 1. Przebieg sprawności zespołu pompy zasilającej kocioł w bloku 200 MW w zależności od wydajności.
3. MOŻLIWOŚCI POPRAWY SPRAWNOŚCI POMP ZASILAJĄCYCH.
3.1. Zwiększenie sprawności początkowej pompy.
Najprostszą możliwością jaka się nasuwa byłoby zastosowanie pomp o sprawności wyższej niż wspomniane 81%. Ta z pozoru oczywista możliwość jest jednak mało realna gdyż dla parametrów, jakie tu występują wyższy poziom sprawności jest trudny do uzyskania. W monografii [1] można znaleźć wykresy pokazujące jakiej sprawności można oczekiwać od pompy w zależności od jej wydajności i wyróżnika szybkobieżności. Wynika z nich, że dla pomp o parametrach odpowiadających pompom zasilającym kocioł 200 MW poziom 81% sprawności jest poziomem oczekiwanym i dobrym w skali światowej. Być może w ofercie niektórych producentów pomp dałoby się znaleźć pompy o nieznacznie wyższej sprawności lecz ewentualne różnice są niższe niż dopuszczalne tolerancje dla sprawności konkretnego egzemplarza [3], więc nie ma pewności, że dostarczona pompa wykaże sprawność w pełni odpowiadającą ofertowej. Wynika z tego, że zamiana typu pompy nie jest efektywnym kierunkiem, gdyż wymaga znacznych nakładów na zakup pompy i przystosowanie do niej stanowiska, natomiast efekty są nieznaczne i niepewne.
3.2. Zastosowanie pompy 100% zamiast dwu 50%.
Można również rozważać zastąpienie pomp pracujących równolegle 2 x 50% jedną pompą. Rozwiązanie takie może przynieść pewne efekty w nominalnym punkcie pracy. Ze wspomnianych wykresów [1] podających zależność oczekiwanej sprawności od wydajności wynika, że dwukrotne zwiększenie wydajności z poziomu 400 na ok 800 m3/h może przynieść wzrost sprawności o ok. 1-2 %. Zatem również w tym przypadku uzyskany wzrost sprawności jest nieznaczny, a ponadto poprawa następuje jedynie przy pracy w okolicy parametrów nominalnych. Zastosowanie pompy 100% zamiast dwu 50% powoduje natomiast komplikacje przy regulacji i zwiększenie energochłonności przy pracy bloku z obniżoną mocą, o czym mowa niżej.
3.3. Zastosowanie energooszczędnego silnika.
Sprawność silników dużej mocy w okresie gdy budowane były bloki 200 MW znajdowała się na poziomie 94%. Obecnie dostępne są silniki energooszczędne, których sprawność przy tych parametrach sięga 97%. Celowe jest zatem rozważanie zastępowania wyeksploatowanych silników silnikami nowymi jako alternatywy dla ich remontu.
3.4. Gospodarka remontowa.
Należy zadać sobie pytanie czym tłumaczy się, stwierdzona (p.2) dziesięcioprocentowa różnica w pobliżu wydajności nominalnej, pomiędzy oszacowaną na podstawie pomiarów sprawnością zespołu pompowego a sprawnością oczekiwaną dla nowej pompy i silnika, która powinna być na poziomie 76%.
Po pierwsze sprawność 76% wynika z przemnożenia sprawności pompy i silnika i nie uwzględnia sprawności pracującego pomiędzy nimi sprzęgła hydrokinetycznego. Nawet pracując bez redukcji prędkości, przy minimalnym poślizgu sprzęgło hydrokinetyczne posiada sprawność na poziomie 97%. Wobec tego sprawność zespołu pompowego ze sprzęgłem hydrokinetycznym w punkcie nominalnym można oszacować jako 0.81 x 0.97 x 0.94 = 73.8%. Większy spadek sprawności przy pracy z wydajnością nominalną występuje gdy pompa dobrana jest z nadmiarem parametrów. W takim przypadku, nawet przy pracy bloku pod pełnym obciążeniem, na sprzęgle hydrokinetycznym następuje zmniejszenie prędkości obrotowej, co powoduje znaczny wzrost strat. Nadmierny zapas parametrów pompy jest zatem szkodliwy z punktu widzenia zużycia energii. Niekorzystny wpływ sprawności sprzęgła hydrokinetycznego na sprawność zespołu jest znacznie większy przy pracy na obniżonych parametrach, o czym mowa poniżej.
Nawet przy uwzględnieniu straty na sprzęgle hydrokinetycznym pomiędzy sprawnością oczekiwaną a zmierzoną występuje znaczna różnica, której nie da się wytłumaczyć inaczej niż przez obniżkę sprawności początkowej na skutek pogorszenia stanu technicznego maszyn.
Z pomiarów parametrów pomp zasilających pracujących w elektrowniach wynika, że aktualne sprawności pomp są nierzadko na poziomie 70% (wobec 81% dla pompy nowej), a w krańcowych przypadkach znanych autorowi, spotyka się pompy osiągające sprawność maksymalną nie przekraczającą 60%.
Wskazuje to na fakt, że dla poziomu energochłonności pomp zasilających mniejsze znacznie mają różnice w sprawności pomp nowych, które w zależności od producenta i jakości danego egzemplarza zawierają się najczęściej w przedziale 80-82%. Decydujące znaczenie ma natomiast sprawność eksploatacyjna, obniżona w stosunku do wyjściowej na skutek zużycia. Jak wspomniano, sprawności pomp znajdujących się eksploatacji mogą znajdować się w przedziale nawet 60-70%.
Dla pompy pracującej na parametrach Q = 450 m3/h, H = 1800 m przy ciężarze właściwym wody 9400 N/m3 , które to parametry odpowiadają parametrom 50% pomp zasilających blok 200 MW pracujący przy pełnej mocy, moc hydrauliczna (czyli minimalna moc na wale pompy wymagana na podstawie praw fizyki) wynosi 2115 kW. Jeśli pompa posiada sprawność 81 % to rzeczywisty pobór mocy wyniesie 2611 kW, natomiast przy sprawności 70% wyniesie 3021 kW. Jak z tego wynika, ze względu na pogorszony stan techniczny zwiększenie poboru mocy z powodu pogorszenia stanu technicznego pompy zasilającej może być na poziomie 400 kW, co przy pracy przez ok 7000 godzin w roku daje różnicę zużycia energii około 2800 MWh na pompę (a pracują jednocześnie dwie). Koszt tej dodatkowej energii przekracza koszt remontu kapitalnego pompy.
Eliminacja lub przynajmniej zmniejszenie tych dodatkowych strat jest możliwe dzięki odpowiedniej polityce remonto-wej. Poprzez naturalne zużycie postępujące na przestrzeni kilku lat można wytłumaczyć kilkuprocentowy spadek sprawności. Jeśli natomiast pompa wykazuje sprawność na poziomie 70% lub niżej, to sugeruje to iż była remontowana w nie-właściwy sposób, przy zastosowaniu części zamiennych nieodpowiedniej jakości, co spowodowało obniżkę sprawności. Decyzję o skierowaniu pompy zasilającej do remontu kapitalnego podejmuje się zazwyczaj na podstawie monitoringu tzw. parametrów ruchowych (drgania, temperatury itp.). Biorąc pod uwagę fakt, że koszt remontu jest niższy od kosztu dodatkowej energii zużywanej na skutek obniżenia sprawności częstotliwość remontów można by ustalać na podstawie monitoringu sprawności energetycznej, tak aby utrzymać sprawność eksploatacyjną pompy w pobliżu sprawności pompy nowej.
Dodatkowo należy zalecić stosowanie w polityce remontowej następujących zasad:
a) Przy wybieraniu wykonawcy remontu nie należy kierować się jedynie ceną lecz również, a raczej przede wszystkim efektem w postaci poziomu sprawności energetycznej uzyskanej po remoncie,
b) Kryterium odbioru remontu powinno być badanie parametrów pompy na stacji prób pozwalające na pomiar sprawności, jaką pompa uzyskuje po remoncie.
3.5. Regulacja parametrów.
Jak stwierdzono wyżej widoczne na rys.1 obniżenie sprawności zespołu pompowego dla wydajności nominalnej z oczekiwanego poziomu 74% do ok. 66% daje się wytłumaczyć pogorszonym stanem technicznym pompy. Podobnego rzędu efekt pogorszenia sprawności z tego powodu występuje w całym zakresie wydajności. Jak jednak widać na rys.1 przy zmniejszeniu wydajności następuje dalszy spadek sprawności zespołu, nawet do poziomu 45% przy wydajności obniżonej do połowy nominalnej co jest konsekwencją zmiany parametrów w stosunku do nominalnych, wymuszonej przez pracę bloku z obniżoną mocą.
Pompy zasilające kotły regulowane są zazwyczaj przez zmianę prędkości obrotowej. Jest to metoda regulacji zazwyczaj najlepsza pod względem efektów energetycznych, jednak w tym przypadku nie zapobiega wzrostowi strat. Jak opisano w [4], przy zmianie prędkości obrotowej dany punkt na charakterystyce pompy przesuwa się w taki sposób, że wydajność spada proporcjonalnie do prędkości obrotowej, a wysokość podnoszenia proporcjonalnie do jej kwadratu. Sprawność przy tym nie ulega w przybliżeniu zmianie. Jeśli taką metodą narysowane zostaną charakterystyki pompy przy różnych prędkościach obrotowych, to punkty o jednakowych sprawnościach leżą na parabolach (rys.2). Parabole te w teorii wychodzą z początku układu współrzędnych, jednak w praktyce poniżej pewnej prędkości obrotowej, zbyt mocno obniżonej w stosunku do nominalnej, teoria ta przestaje mieć zastosowanie gdyż następuje tam głębszy spadek sprawności. Z tego powodu na rys.2 pokazano jedynie fragment wykresu dla wyższych prędkości obrotowych, gdzie paraboliczny kształt linii stałej sprawności odpowiada rzeczywistości.

Rys. 2. Współpraca pompy regulowanej przez zmianę prędkości obrotowej z układem o płaskiej charakterystyce.
Regulacja przez zmianę prędkości obrotowej jest najskuteczniejsza wtedy gdy parabola najwyższej sprawności pokrywa się z charakterystyką układu. Taka sytuacja jest możliwa w układach obiegowych (np. ciepłowniczych) gdzie nie występuje statyczna wysokość podnoszenia. Natomiast charakterystyka układa zasilania kotła jest płaska. Wynika to z tego, że wymagane jest wysokie ciśnienie zasilania kotła, do którego dochodzą straty w rurociągach rosnące, teoretycznie, z kwadratem wydajności lecz posiadające niższy rząd wielkości niż ciśnienie zasilania. Przykład charakterystyki układu zasilania kotła, czyli zależności wymaganej wysokości podnoszenia pompy od wydajności pokazano na rys. 3. Jest to charakterystyka wyliczona na podstawie tych samych danych pomiarowych co sprawność zespołu na rys.1. Jak widać z rys.3 ciśnienie zasilania (odpowiadające wysokości podnoszenia przy zerowej wydajności) jest na poziomie powyżej 1400 m. Ze wzrostem wydajności na skutek strat przepływu wysokość podnoszenia wzrasta do poziomu 1800 m. Poszczególne punkty pomiarowe wykazują rozrzut typowy dla pomiarów przemysłowych ale generalnie układają się zgodnie z teorią w pobliżu paraboli. (Dla porządku należy dodać, że charakterystyka tego układu może ulegać zmianie na skutek zmiany jego konfiguracji, np. pobierania wody do wtrysków).

Rys. 3. Charakterystyka układu pompy zasilającej określona na podstawie wyników pomiarów (dane dla jednej z dwu pomp pracujących równolegle).
W tym miejscu należy zwrócić uwagę, że jedną z możliwości redukcji zużycia energii do napędu pomp jest redukcja strat w rurociągu, np. przez stosowanie armatury (zaworów, filtrów itp.) o niższych współczynnikach oporu. Jest to oczywiste, lecz pozostaje poza zakresem niniejszego artykułu koncentrującego się na pompach.
Jak widać z rys. 3 z charakterystyki rurociągu wynika, że pompy zasilające kocioł przy pełnej wydajności odpowiadającej pracy bloku z pełną mocą muszą wytwarzać wysokość podnoszenia rzędu 1800 m, natomiast przy pracy z wydajnością ograniczoną o połowę wysokość podnoszenia spada do poziomu 1500 m. Jak pokazano poglądowo na rys. 2 przy regulacji przez zmianę prędkości obrotowej powoduje to, że pompy wychodzą z obszaru optymalnych sprawności. Położenie punktu optymalnej sprawności przesuwa się wzdłuż osi wydajności proporcjonalnie do prędkości obrotowej. Zatem, aby optymalna sprawność wystąpiła przy połowie wydajności nominalnej obroty powinny zmniejszyć się do połowy. Jednak przy płaskiej charakterystyce układu w celu obniżenia wydajności do połowy potrzebne jest zmniejszenie obrotów w mniejszym stopniu i punkt optymalnej sprawności nie przesuwa się po charakterystyce wraz z punktem pracy lecz pozostaje na wyższych wydajnościach.
Oprócz pogorszenia sprawności pompy wynikającego z jej charakterystyki regulacyjnej następuje pogorszenie sprawności napędu. Przy znacznym spadku poboru mocy wynikającym z obniżenia wydajności pogarsza się sprawność silnika w związku z jego niedociążeniem. Nie jest to jednak spadek znaczący i z reguły zawiera się w zakresie 1-2 %. Poważniejsze straty występują na sprzęgle hydrokinetycznym. Na rys.4 pokazano sprawności napędów z regulowaną prędkością obrotową wg [2]. Przy regulacji z zastosowaniem przetwornika częstotliwości straty są stosunkowo niewielkie w szerokim zakresie prędkości obrotowych. Natomiast dla tradycyjnego sprzęgła hydrokinetycznego sprawność szybko spada ze zmniejszaniem obrotów.
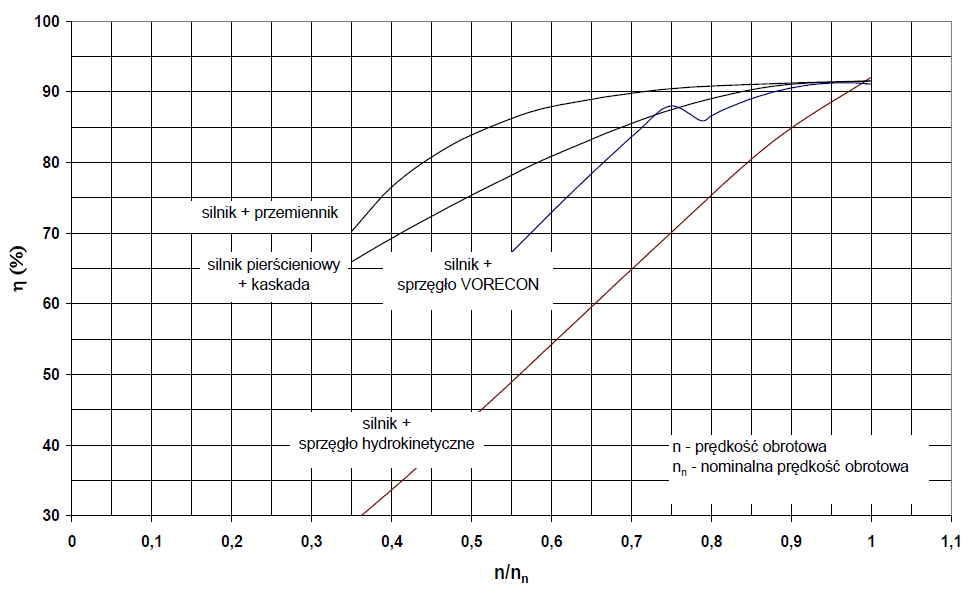
Rys. 4. Porównanie sprawności napędów o regulowanej prędkości.
Typowy zespół pompy zasilającej w bloku o mocy 200 MW według struktury z lat 70-tych XX w., kiedy bloki te były projektowane i budowane, składał się z pompy wielostopniowej napędzanej silnikiem elektrycznym przez przekładnię podnoszącą obroty oraz sprzęgło hydrokinetyczne służące do regulacji parametrów. Dostępne w tamtym czasie rozwiązania techniczne narzucały określone uwarunkowania doboru pomp. Regulacja poprzez sprzęgło hydrokinetyczne możliwa była jedynie w dół. W celu zapewnienia możliwości kompensacji obniżki parametrów na skutek zużycia pompy dobierane były z pewnym zapasem wysokości podnoszenia. Było to niekorzystne z punktu widzenia energetycznego gdyż na skutek tego zespoły pompowe pracowały ze zwiększonym poślizgiem na sprzęgle hydrokinetycznym, co powodowało wzrost strat w sprzęgle. Kwestia regulacji nie była jednak kwestią o zasadniczym znaczeniu, gdyż w tamtym okresie bloki pracowały z reguły z obciążeniem bliskim maksymalnemu.
Obecnie bloki energetyczne o mocy 200 MW pracują w szerokim zakresie obciążeń, w tym stosunkowo często przy połowie mocy nominalnej, co powoduje konieczność ograniczenia wydajności pomp również do około połowy. Rozpatrzmy dla przykładu pracę pomp na parametrach zarejestrowanych w rzeczywistości jak na rys 3. Są to zmierzone parametry jednej z dwu pomp pracujących równolegle, a zatem całkowita wydajność podawana przez pompy do kotła jest dwukrotnie większa niż na wykresie. Jak widać parametry koncentrują się wokół dwu typowych punktów pracy: Q = 760 m3/h i H =1730 m oraz Q = 400 m3/h i H =1500 m. Na rys. 5 pokazano typową, przykładową charakterystykę pompy 100% dobranej na punkt Q = 760 m3/h i H =1730 m, które to parametry pompa osiąga przy prędkości obrotowej ok. 4050 obr/min. Sprawność w tym punkcie wynosi 81%. Jeśli na skutek zmniejszonego obciążenia bloku zachodzi potrzeba ograniczenia wydajności do 400 m3/h, a z charakterystyki układu wynika, że wysokość podnoszenia przy tej wydajności wynosi 1500 m, to jak widać z rys. 5, aby osiągnąć te parametry prędkość obrotowa pompy powinna być zredukowana do ok. 3450 obr/min. Sprawność w takim punkcie pracy wyniesie 70%. Jak widać z rys. 4, przy takim stopniu redukcji prędkości obrotowej sprawność napędu z tradycyjnym sprzęgłem hydrokinetycznym wyniesie 80%, a całkowita sprawność zespołu pompowego 0.7 x 0.8 = 56 %. Pobór mocy przy Q = 400 m3/h i H = 1500 m wyniesie 2798 kW (zakładając gęstość 9400 kg/m3 jak dla typowej temperatury wody zasilającej).
Straty można ograniczyć zastępując regulację przez sprzęgło hydrokinetyczne starego typu regulacją przez przetwornik częstotliwości. Jak wynika z rys.4 sprawność napędu z przetwornikiem wyniesie ok. 92%, a sprawność zespołu pompowego 73.6%. Zastąpienie sprzęgła hydrokinetycznego falownikiem wymaga jednak znacznych nakładów inwestycyjnych.
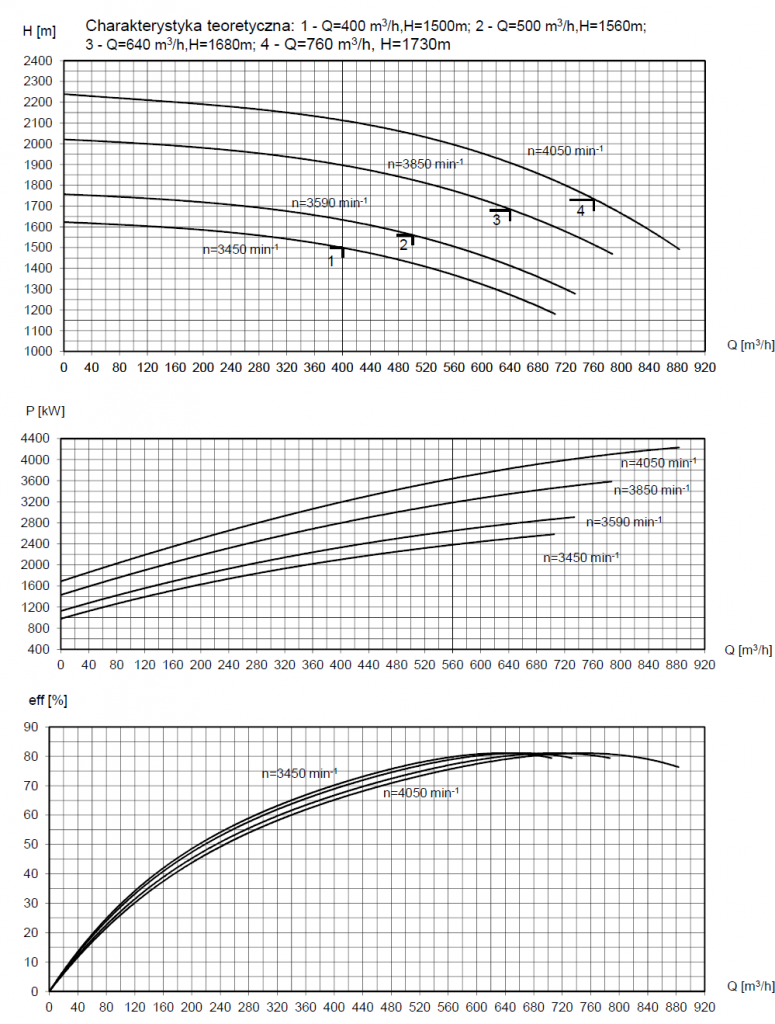
Rys. 5. Regulacja pracy pompy 100%.
Należy podkreślić, że jakościowo z taką samą sytuacją mamy do czynienia jeśli zamiast pompy 100 % jak w powyższym przykładzie pracują łącznie dwie pompy 50%. Ich łączna charakterystyka, powstała ze zsumowania wydajności obu pomp przy danej wysokości podnoszenia, pokazana na rys. 6 jest zbliżona do charakterystyki pompy 100% i zachowuje się w podobny sposób przy regulacji przez zmianę prędkości obrotowej. W tym wypadku aby obniżyć wydajność z 760 na 400 m3/h należy obniżyć prędkość obrotową z 3490 na 3060 obr/min (do 87.6%). Sprawność pomp na zredukowanych obrotach przy wydajności 400 m3/h wyniesie 70 %. Ze względu na nieco niższy stopień redukcji prędkości obrotowej (87.6%) sprawność napędu z tradycyjnym sprzęgłem hydrokinetycznym wyniesie ok 83%, a sprawność całego zespołu pompowego 0.7 x 0.83 = 58.1 %. Pobór mocy przy Q = 400 m3/h i H =1500 m wyniesie zatem 2696 kW.
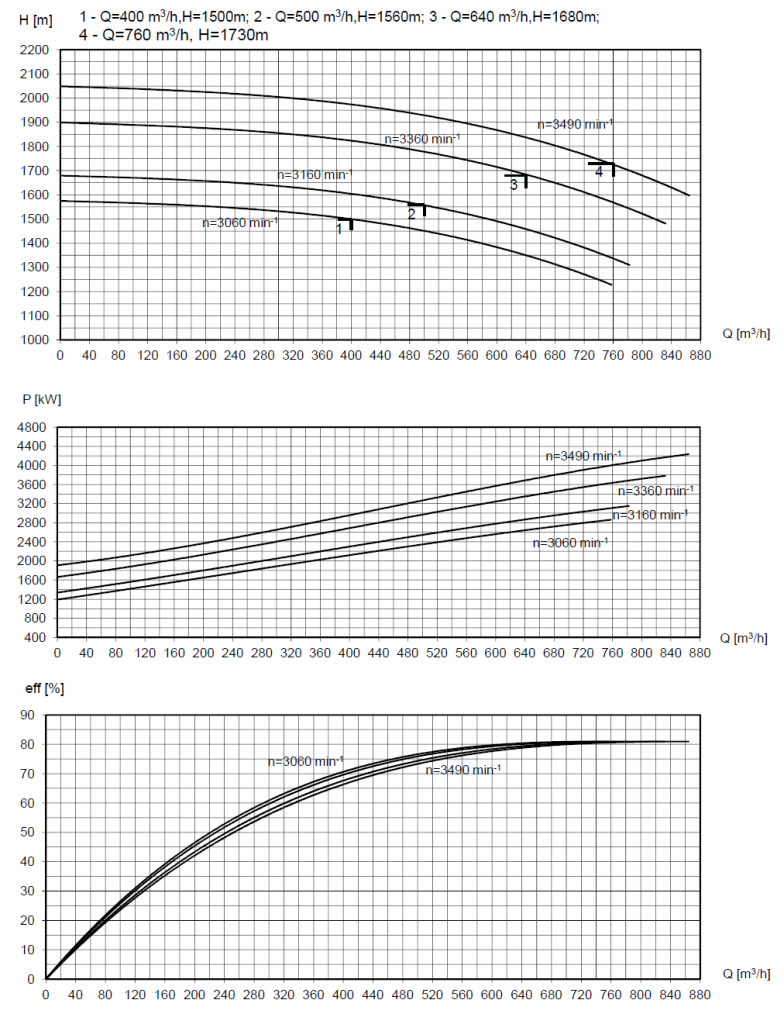
Rys. 6. Regulacja dwu pomp 50% pracujących równoległe.
Gdyby więc, co jest częstą praktyką, przy obniżaniu mocy bloku regulować wydajność przez zmniejszanie obrotów obu pomp jednocześnie, to również w takim przypadku sprawność zespołu spadnie do podobnego poziomu jak dla pompy 100%. Jeśli jednak dysponujemy układem pomp 2 x 50% to przy redukcji wydajności do poziomu 50% zamiast ograniczać wydajność obu pomp jednocześnie, można jedną z pomp wyłączyć i uzyskać wymaganą wydajność z jednej pompy, która pracuje wtedy w pobliżu swojej wydajności nominalnej. Sytuacja taka pokazana jest na rys. 7. Pracująca samodzielnie pompa uzyska Q = 400 m3/h i H =1500 m przy prędkości obrotowej ok. 3350 obr/min, a zatem zredukowanej w stosunku do prędkości przy pracy równoległej w punkcie Q = 760 m3/h i H =1730 m w stosunku 3350/3490 = 0.96.
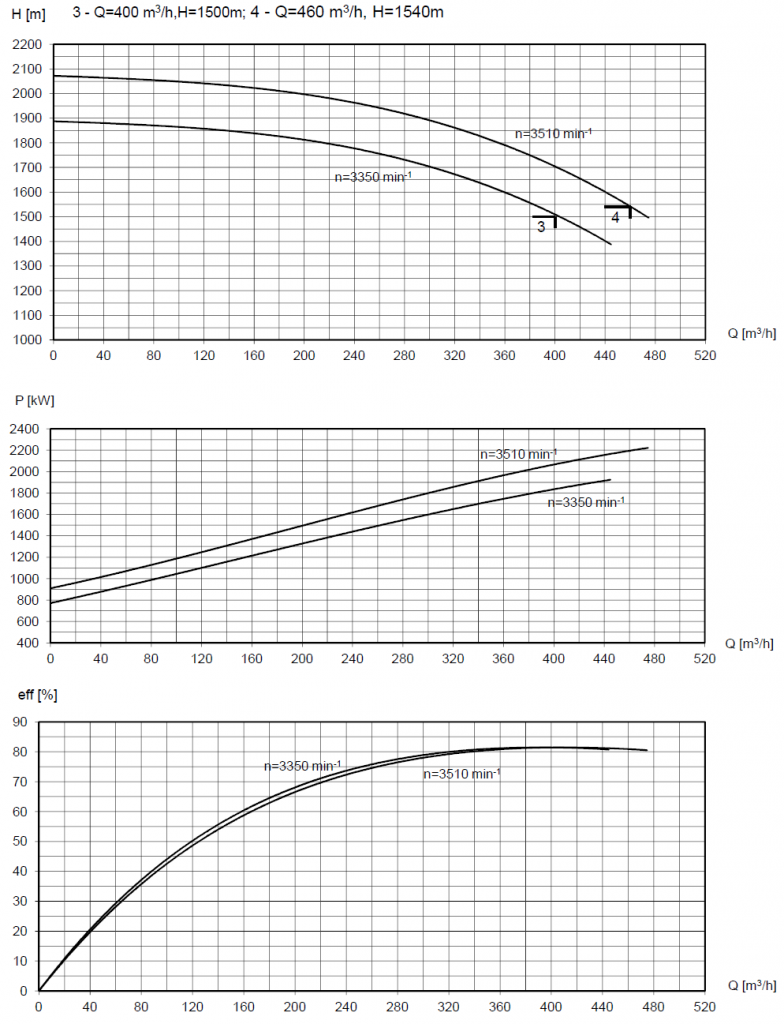
Rys. 7. Praca pojedynczej pompy 50%.
Pompa pracując pojedynczo w punkcie Q = 400 m3/h i H =1500 m uzyska sprawność 81%, a napęd przez tradycyjne sprzęgło hydrokinetyczne uzyska przy danej redukcji prędkości obrotowej sprawność ok. 89%. W rezultacie sprawność zespołu pompowego wyniesie 0.81 x 0.89 = 72.1%, a pobór mocy 2173 kW. Jak widać zmiana sposobu regulacji polegająca na wyłączeniu jednej z dwu pomp zamiast równomiernego obniżania wydajności dwu pomp pracujących równolegle pozwala obniżyć pobór mocy przy obniżonej wydajności o ponad 500 kW. Jest to oszczędność nie wymagająca żadnych inwestycji, a jedynie zmiany sposobu eksploatacji. Dla porządku należy zaznaczyć, że częste wyłączanie jednej z pomp w pewnym stopniu skraca jej okres międzyremontowy, gdyż każdy rozruch i zatrzymanie jest dla pompy stanem niekorzystnym. Efekt ten nie niweluje jednak możliwych do uzyskania korzyści energetycznych.
Powyższe przykładowe obliczenia przeprowadzono na wybranych charakterystykach pomp o typowym przebiegu i dla punktów pracy stwierdzonych w rzeczywistej elektrowni. Dla innych typów pomp i innych parametrów pracy bloku wyniki mogą się różnić ilościowo, lecz w mocy pozostają ważne wnioski jakościowe, które sformułowano niżej w podsumowaniu.
Powyższe rozważania dotyczące regulacji wydajności dla przejrzystości przeprowadzono na charakterystykach jak dla pomp nowych. Efekt pogorszenia sprawności w trakcie eksploatacji, o którym była mowa wyżej nakłada się na zjawiska związane z regulacją.
4. PODSUMOWANIE I WNIOSKI.
1. Na poziom zużycia energii przez pompy zasilające kocioł bloku energetycznego zasadniczy wpływ ma aktualna sprawność energetyczna pomp, która jak wskazują pomiary w wielu przypadkach zasadniczo odbiega od sprawności pomp nowych. W celu ograniczenia poważnych strat energii wynikających z te-go zalecana jest odpowiednia polityka remontowa uwzględniająca następujące zasady:
a) Pompy powinny być kierowane do remontu nie wy-łącznie na podstawie kryteriów ruchowych lecz na podstawie monitoringu sprawności energetycznej
b) Kryterium wyboru wykonawcy remontu (obok ceny) powinna być w pierwszym rzędzie sprawność ener-getyczna uzyskana po remoncie, która powinna być weryfikowana w trakcie pomiarów na stacji prób po wykonanym remoncie.
2. Dla bloków pracujących w szerokim zakresie zmian mocy (np. w dół do 50 % mocy nominalnej) znaczne oszczędności energetyczne przy pracy z obniżoną wydajnością można uzyskać zastępując sprzęgła hydrokinetyczne starego typu przez nowocześniejsze napędy regulowane, np. przetwornice częstotliwości. Wymaga to jednak nakładów inwestycyjnych, których okres zwrotu powinien być oszacowany przed podjęciem decyzji.
3. Znaczne oszczędności energetyczne można uzyskać bez nakładów inwestycyjnych zmieniając sposób eksploatacji pomp pracujących w układzie równoległym 2 x 50%. Wyłączając jedną z pomp zamiast ograniczania wydajności dwu pomp pracujących równolegle można uzyskać bardzo istotną poprawę sprawności w zakresie wydajności 50-60% maksymalnej.
4. Układ pomp 2 x 50% jest znacznie bardziej elastyczny pod względem regulacji niż jedna pompa 100% w układach o płaskiej charakterystyce, do jakich należy układ zasilania kotła bloku energetycznego. Pomimo tego, że pompa 100% jest w stanie uzyskać nieco wyższą sprawność w okolicy wydajności maksymalnej, dla bloków pracujących często z mocą obniżoną do poziomu 50% mocy maksymalnej zaleca się stosowanie układu pomp 2 x 50%. Pozwala to przy wyłączeniu jednej z pomp na pracę przy wydajności kotła z zakresu 50-60% nominalnej ze sprawnością bliską maksymalnej, co nie jest możliwe do uzyskania przy pompie 100%.
5. Dawna praktyka polegająca na doborze pomp na maksymalne parametry i regulacji wyłącznie w dół nie jest obecnie optymalna. Obecnie dostępne są sposoby regulacji umożliwiające również zwiększanie parametrów. Przy ich wykorzystaniu korzystne jest dobieranie pomp na parametry takie, na jakich najczęściej pracują (niekoniecznie maksymalne) gdyż wtedy uzyskuje się najwyższą sprawność w najczęściej występującym punkcie pracy. Dobór oparty na takiej zasadzie wymaga analizy dla każdego przypadku, której podstawą są dane o przewidywanym rozkładzie godzinowym parametrów pracy bloku.
Dr inż. Grzegorz Pakuła
Literatura:
- W. Jędral, Pompy Wirowe, Wydawnictwo Naukowe PWN, Warszawa 2001,
- W. Misiewicz, A. Misiewicz, Napędy regulowane w układach pompowych źródeł ciepła, Krajowa Agencja Poszanowania Energii SA, Warszawa 2008
- G. Pakuła, Sprawność ofertowa pomp, Pompy Pompownie, nr 2/2012
- G. Pakuła, Regulacja wydajności dwu pomp pracujących równolegle, Pompy Pompownie, nr 3/2011